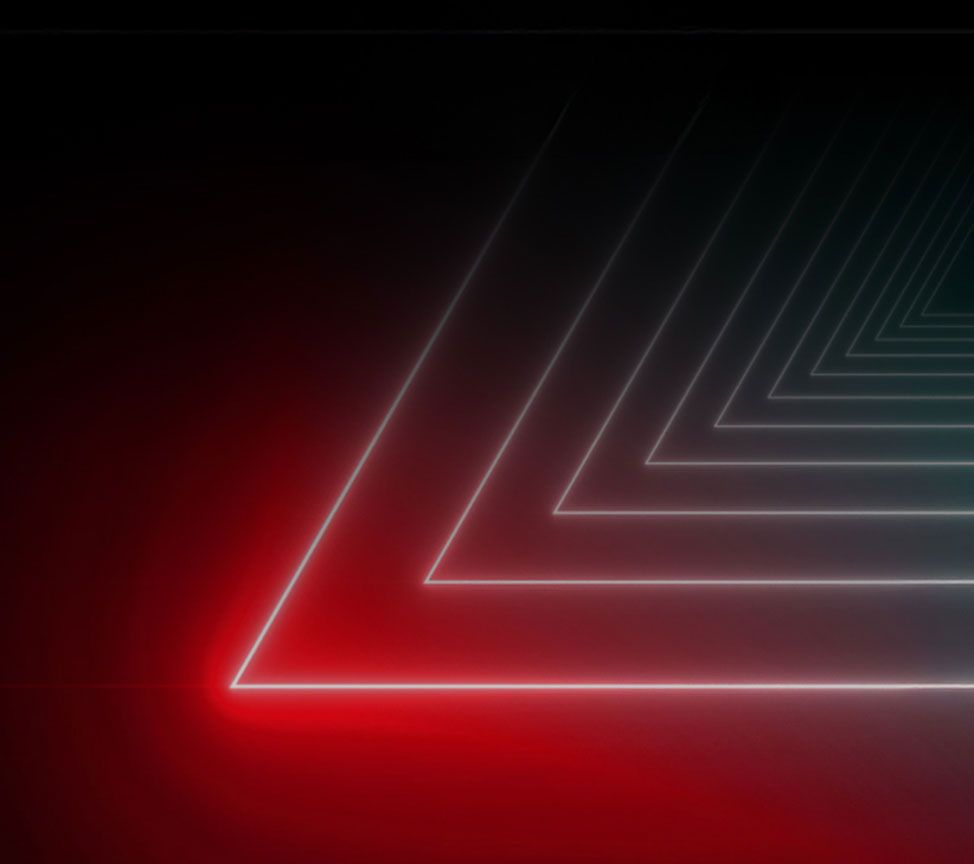
247Tailorsteel enables its customers to order tailormade steel constructions online. Previously, customers of 247TailorSteel would have to install a software package, which wouldn't work on all systems. TRIMM and 247TailorSteel brought this application to the web with a fast and user-friendly application that runs on almost every modern system and price winning user experience (UX) as result.
247TailorSteel
User Experience and software development
User Experience
Architecture
Application Development
Data Services
Development Team
Consultancy
How can a fusion of a great customer experience and new techniques lead to optimal results?
Working with a Windows application that had to be installed by (potential) customers to submit orders was a hurdle in delivering an excellent user experience. 247TailorSteel sought a way to streamline the process in all (future) factories for expansion and synergy. The application needed to be scalable and work efficiently across all factories. This way, orders should automatically be produced and delivered to the right location quickly and accurately. Starting this process with laser cutting and bending, aiming to lead the processing market.
Coming from Sophia® an installable desktop application that was locked to a single operating system, it was clear that there were a few hurdles to take to scale up and streamline the ordering process, to make sure that 247TailorSteel’s new factories could live up to their full potential.
247TailorSteel realized that the best way to tackle these hurdles and scale up and streamline the ordering process was to move to the cloud. Making this move would mean easier scalability and an opportunity to elevate the customer experience at the same time.
To bring Sophia® to the cloud, 247TailorSteel called upon the help of TRIMM. The teams of TRIMM and 247TailorSteel worked together seamlessly to create a new customer-centric online platform to fulfill the capabilities of the original application – and then some.
Users are now able to simply drop a 3D file into their browser and get to work, with real-time feedback when choosing materials and finishing options. Feasibility checks are now done on the fly with each change as opposed to after requesting a quote. All the clients’ choices are reflected in the form of an interactive 3D representation of their project, right there in the browser. The entire ordering process has been streamlined and sped up to allow clients to pick their desired delivery date and re-order with a few clicks. Ensuring that the entire process is now running at speeds that far exceed what the desktop application was capable of.
The new cloud infrastructure allows 247TailorSteel to iterate much faster and to keep growing the functionality of Sophia® for Web. Right now, this has already enabled them to add multiple new product options to the cloud platform that could not have been achieved in the desktop application with the same ease.
The use of partial deliveries, which were validated at every step, created a highly useful product within a short period of time. During this process, we have intensive collaboration with each other, which is an important key to success. By empowering the team, the complex technical environment, materials, and customer needs were translated into the correct insights for the new platform. This ensured a well-performing tool for 247TailorSteel!
Placing orders is now effortless, due to automation and efficiency according to the way of working. Meaningful intensive collaboration emerged by working closely with the client, their clients, and stakeholders. Involving users and stakeholders in the design process led to high satisfaction. Moreover, they wholeheartedly embraced the new application because it simplified their lives and offered full control and visibility over their orders. The user experience remains paramount, preserving what works flawlessly while innovating where necessary.
247Tailorsteel’s journey showcases how optimizing the user experience is not just a benefit but a driving force behind achieving operational excellence.
‘Sophia® is quick and easy for optimal ordering convenience, 24 hours a day!’
‘In the new version of Sophia®, it's great that you can group issues by project. Also for colleagues in sales of standard cyclical components, it is convenient that they do not have to upload designs every time. In fact, these are already stored in the web app's overview and can be easily retrieved.’
‘With just one click, you have access to the most advanced laser cutting machines and press brakes. We save an enormous amount of time thanks to Sophia®. This allows us more scope for acquisition, maintaining customer relationships and building connections. We can offer customers very competitive quotes at lightning speed, leaving a strong impression.’
The new cloud infrastructure allows 247Tailorsteel to iterate much faster and to keep growing the functionality of Sophia® for Web. Right now, this has already enabled them to add multiple new product options to the cloud platform that could not have been achieved in the desktop application with the same ease.
The Dutch Interactive Awards is a sought after accolade for companies driving digital developments to the core of their business. 247TailorSteel and TRIMM received a raving jury report for their UX implementation of Sophia®.
Jury report:
“From Windows 98 to a web application. Outdated software has been replaced through a digital transformation, directly integrated with the high-tech factory. A super-fast order process was achieved through improved UX, with a significant impact thanks to digital transformation across all facets of the organization in a traditional market. The impact is evident in leads and strong, tangible results. The jury sees enormous growth opportunities here, with a strong customer-centric approach. That’s why this is rightfully the gold winner.”
Making your customers' lives easier through an optimal user experience, digitizing processes or innovating with a cloud-based solution. Challenge us, we like to think along with you!
You can contact Marc Woesthuis through the form below, or through the following number +31 (0)53 4800 480